Welcome to the Blachford Acoustics Laboratory and Technical Center
The only laboratory specifically designed for testing both smaller vehicles and products, as well as large equipment such as heavy trucks, off-highway machines, buses or motor homes.
ANAB accredited ISO/IEC 17025 Testing Laboratory
ASTM C423
Random Incidence Sound Absorption Coefficient
ASTM E1050
Normal Incidence Sound Absorption Coefficient
ASTM C522
Airflow Resistance of Acoustical Materials
ASTM C518
Steady-State Thermal Transmission
SAE J1400
Sound Transmission Loss
Product Testing Capabilities:
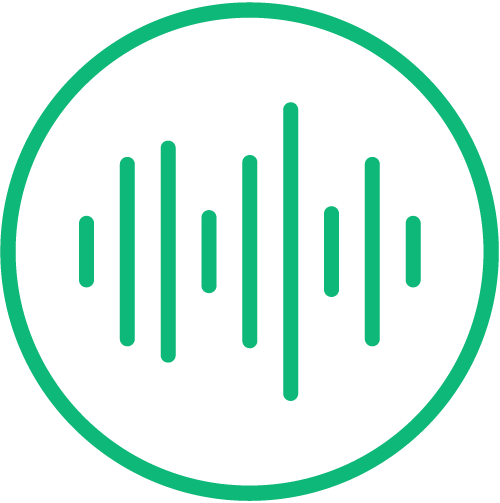
Sound Quality
Our in-house Acoustics Lab is the only lab specifically designed for testing small vehicles and products, as well as large equipment such as trucks, off-highway machines, buses, or RVs.
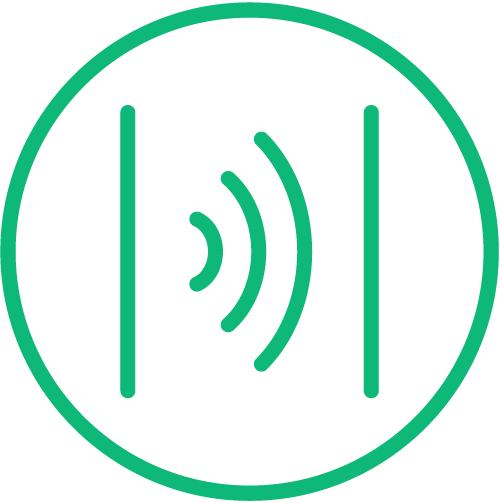
Noise Control Optimization
Our team uses the latest technology to determine your product’s base-line sound levels and will then map all sound sources and paths.
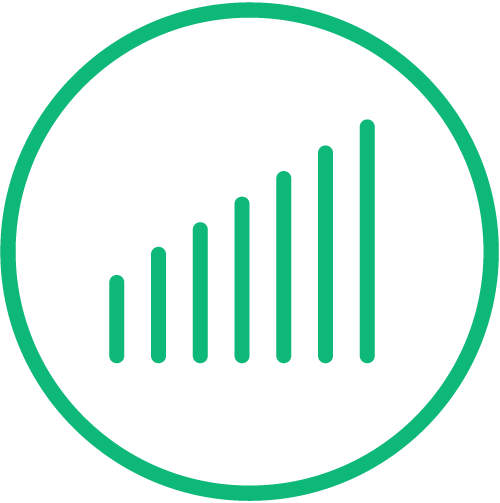
Sound Power
We accurately measure the sound energy from the source, and determine whether or not it meets noise and sound quality goals.
Material Testing Capabilities:
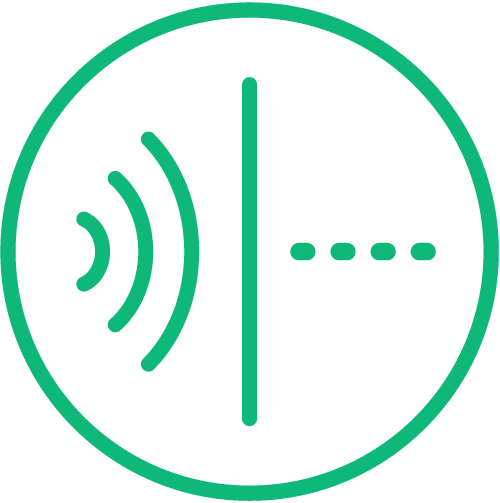
Sound Transmission Loss
We accurately measure the sound energy from the source, and determine whether or not it meets noise and sound quality goals.
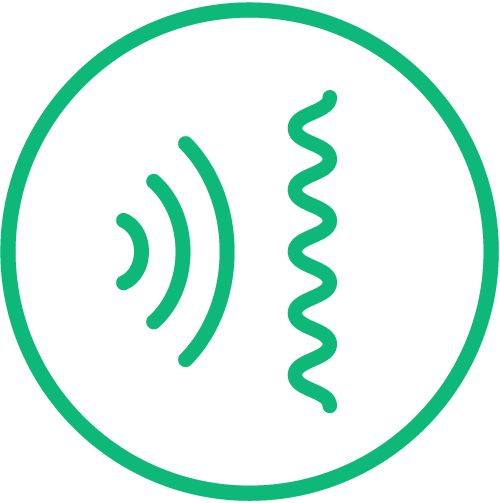
Sound Absorption
Using our in-house, echo-free Hemi-Anechoic Chamber, we can isolate and analyze the acoustical composition and impact of noise structures.
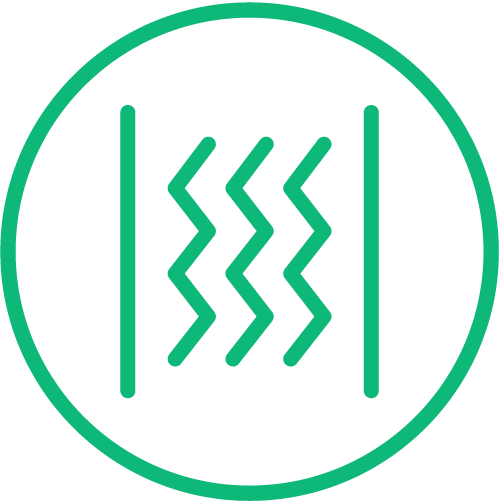
Damping
We test to ensure sheet and Liquid Applied Spray damping solutions meet or exceed noise and vibration absorption requirements.
PERFECTING THE SCIENCE OF SOUND
Industry Leading Testing Facilities
Hemi-Anechoic Chamber
One of the quietest rooms in the world, this is where we will determine base-line sound levels, map all sound sources and paths, and compile all necessary data to solve even the most complicated noise and vibration issues. This massive, drive-in chamber is an echo-free (anechoic), virtually silent environment suitable for testing large vehicles including buses, trucks, construction equipment and more.
Reverberation Room
The exact opposite of our Hemi-Anechoic Chamber, this 7,000 cubic foot chamber designed to reflect sound and used for material and buck testing. The hard, non-porous walls with stationary and rotating sound wave diffusers allow our team of experts to evaluate different acoustic treatments by testing for Sound Transmission Loss (STL), sound absorption, and sound power.
Control Room
Constructed to monitor and control both the Hemi-Anechoic Chamber and the Reverberation Room, here our team of acoustic engineers gather important data, monitor product testing and create sound maps. This detailed analysis provides us with the information we need to create solutions to dampen vibrations and reduce noise.
Outdoor Test Pad
Directly outside the doors of our Hemi-Anechoic Chamber, here our team of engineers gather sound power measurements of large equipment. In addition to the 10-meter hemispherical test surface, the area also features acceleration and deceleration lanes.
Isolation Chambers
Anechoic chambers, constructed with sound absorptive walls and ceiling, that are used as the reviewing room during material sound transmission loss studies.
Testing Room
With equipment to thoroughly run small sample testing, here we perform thermal conductivity, normal incidence sound absorption, air flow resistivity and microscopic examinations.
Buck Chamber Room
A sound isolation chamber that is used as the receiving room during buck studies and other projects using the 8’x8′ test opening. A vehicle or machine component is placed inside the chamber, which connects a quiet room with the reverberation chamber. The component is then sealed in the opening so that sound from the reverberation room only enters the quiet room through the component. A sound intensity scan may then be performed to provide a level of detail not previously possible. This type of test provides a highly repeatable method for part development and optimization.
Jury Room
More than just a conference room, the jury room is where we present and evaluate actual and simulated recordings of the sound from your product. Through this coordinated effort, we gain a better understanding of the sound requirements and attributes of your products, develop models based on sound sources and paths and engineer and product treatments.
PERFECTING THE SCIENCE OF SOUND
Blachford Acoustics: Certified High Quality
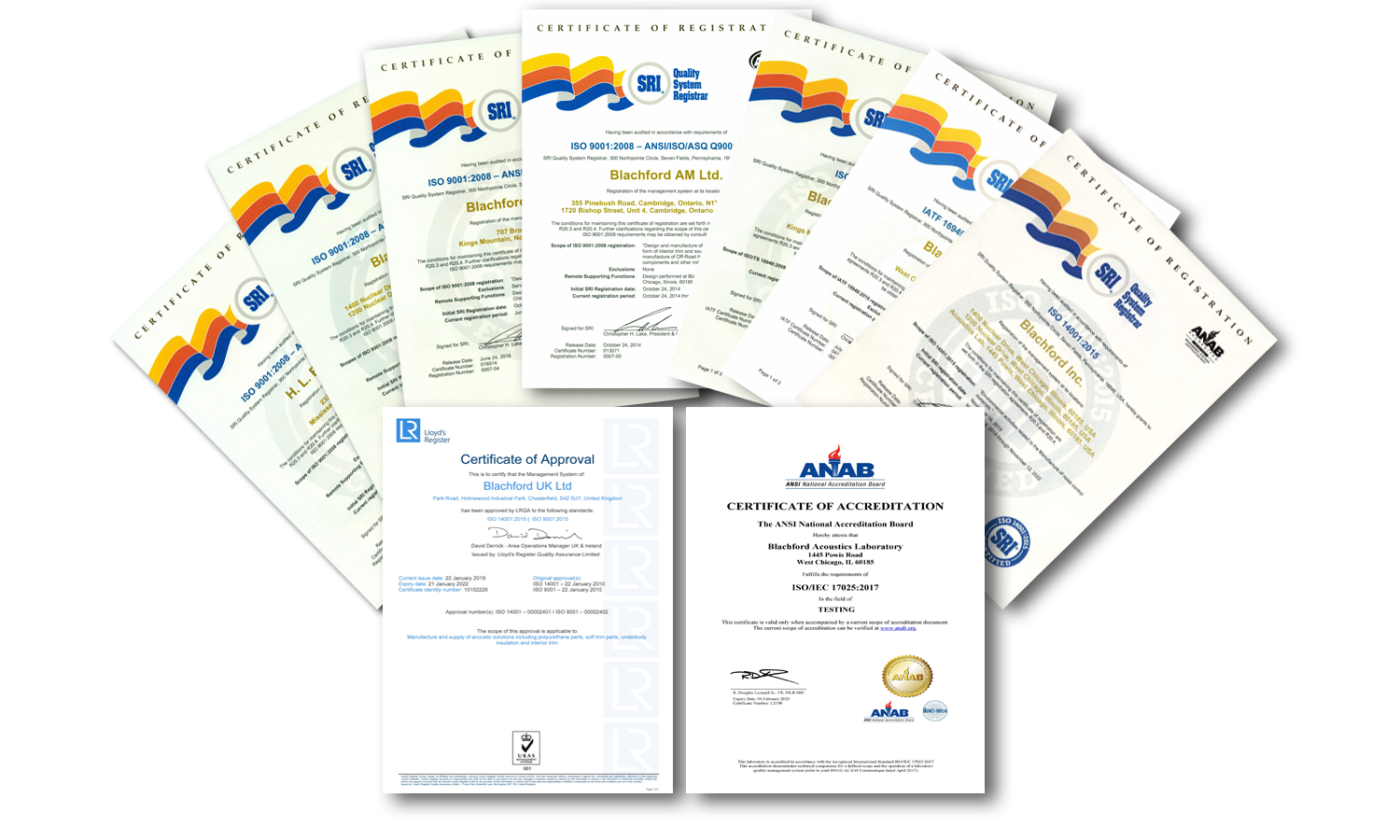
BLACHFORD CERTIFICATES
Blachford Acoustics Lab
ISO/IEC 17025
Blachford Inc.
ISO 9001
IATF 16949
ISO 14001
Milcut Inc.
ISO 9001
Blachford AM
ISO 9001
Blachford RP
ISO 9001
IATF 16949
ISO 14001
Customers Who Trust Blachford Acoustics Group
“Blachford eliminated SKUs. Across product families, the reduction of one SKU is a $10k savings. Blachford eliminated 14 SKUs.”
– Noise Control Research Engineer – Construction Equipment Manufacturer
“The first project with Blachford, it was a definite quality improvement, and it was over a million dollar yearly cost savings for just the purchase parts themselves. We went from 28 (SKU) parts to 14.”
– Design Engineer – Heavy Equipment Manufacturer
“Noise is important to brand image. It is one of the top factors along with driveability and reliability. Acoustics – it’s a 4 out of 5, it might even be a 5 in importance projecting the image, the brand, and the quality that we want projected to the market.”
– Design Engineer – Truck Manufacturer
“Our ten-fold growth prior to our acquisition was expedited by our working relationship with Blachford.”
– Design Engineer
“For our shareholders, we have to produce a product at the lowest cost, at the right level of quality and sell it at the highest price we can. We look for suppliers who can help us do that. Blachford helps us do that.”
– Global Procurement Manager – Construction Equipment Manufacturer
“When a company does a spec, boundary conditions like humidity that day, temperature, that all matters. ASPM national or international spec. We try to verify where we can, but we don’t even have the equipment they have. We trust their specifications. Blachford brings innovative ideas, processes, materials, and offerings we value.”
– Design Engineer – Truck Manufacturer
“Then, bringing them in at the beginning with our new product design, it probably saved 6-12 months of development. We didn’t just wa nt the spec sheet value. We wanted customers to get in the machine and experience the difference.”
– Design Engineer – Heavy Equipment Manufacturer
“If we have an acoustics issue, we will reach out to Blachford since they are the experts. It saves us money because we do not have to keep an acoustic expert on site with an annual salary, with benefits, of $125K.”
– Design Engineer – Truck Manufacturer
“As a mechanical engineer, we make stuff that is practical and affordable and Blachford’s materials routinely help me reach these goals.”
– Design Engineer
“We [purchasing department] reported savings of $100k annually from moving to the die-cut solution using Blachford.”
– Design Engineer – Truck Manufacturer
Customers Who Trust Blachford Acoustics Group
“Blachford eliminated SKUs. Across product families, the reduction of one SKU is a $10k savings. Blachford eliminated 14 SKUs.”
– Noise Control Research Engineer – Construction Equipment Manufacturer
“The first project with Blachford, it was a definite quality improvement, and it was over a million dollar yearly cost savings for just the purchase parts themselves. We went from 28 (SKU) parts to 14.”
– Design Engineer – Heavy Equipment Manufacturer
“Noise is important to brand image. It is one of the top factors along with driveability and reliability. Acoustics – it’s a 4 out of 5, it might even be a 5 in importance projecting the image, the brand, and the quality that we want projected to the market.”
– Design Engineer – Truck Manufacturer
“Our ten-fold growth prior to our acquisition was expedited by our working relationship with Blachford.”
– Design Engineer
“For our shareholders, we have to produce a product at the lowest cost, at the right level of quality and sell it at the highest price we can. We look for suppliers who can help us do that. Blachford helps us do that.”
– Global Procurement Manager – Construction Equipment Manufacturer
“When a company does a spec, boundary conditions like humidity that day, temperature, that all matters. ASPM national or international spec. We try to verify where we can, but we don’t even have the equipment they have. We trust their specifications. Blachford brings innovative ideas, processes, materials, and offerings we value.”
– Design Engineer – Truck Manufacturer
“Then, bringing them in at the beginning with our new product design, it probably saved 6-12 months of development. We didn’t just wa nt the spec sheet value. We wanted customers to get in the machine and experience the difference.”
– Design Engineer – Heavy Equipment Manufacturer
“If we have an acoustics issue, we will reach out to Blachford since they are the experts. It saves us money because we do not have to keep an acoustic expert on site with an annual salary, with benefits, of $125K.”
– Design Engineer – Truck Manufacturer
“As a mechanical engineer, we make stuff that is practical and affordable and Blachford’s materials routinely help me reach these goals.”
– Design Engineer
“We [purchasing department] reported savings of $100k annually from moving to the die-cut solution using Blachford.”
– Design Engineer – Truck Manufacturer
It’s Easy to Get Started
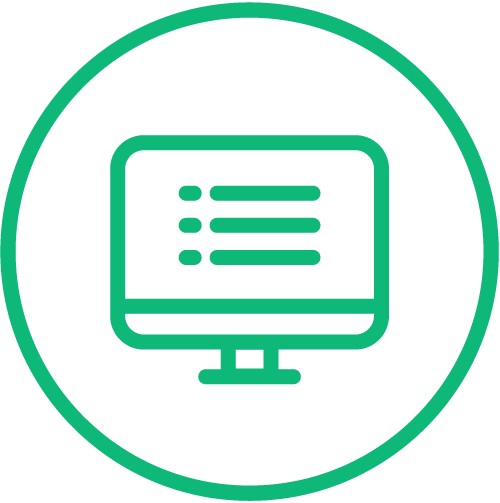
STEP 1:
COMPLETE OUR GET STARTED FORM
Give us some basic information about your sound, vibration or thermal reduction goals.
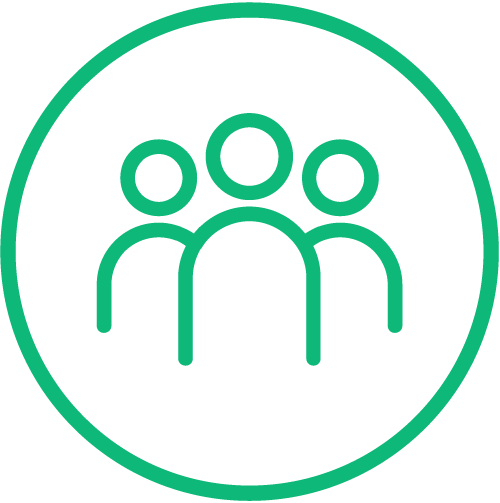
STEP 2:
COLLABORATE WITH OUR EXPERTS
Our team of engineers will work with you to uncover all issues and identify possible solutions.